Understanding the Best Protection Against Corrosion
When it comes to protecting electrical conduit threads from corrosion, choosing the right galvanization method is crucial. Without proper protection, threads can degrade over time, leading to installation challenges, system failures, and costly repairs. Several galvanizing methods exist, each with its own advantages and drawbacks. Understanding these options helps electrical contractors make informed decisions about conduit selection.
What Is Galvanizing and Why Use Zinc?
Galvanizing is the process of applying a protective layer of zinc to steel, shielding it from corrosion. Zinc serves as a sacrificial barrier, preventing rust and deterioration even in the most corrosive environments. For electrical contractors, properly galvanized conduit threads ensure long-term reliability in industrial, marine, and chemical applications.
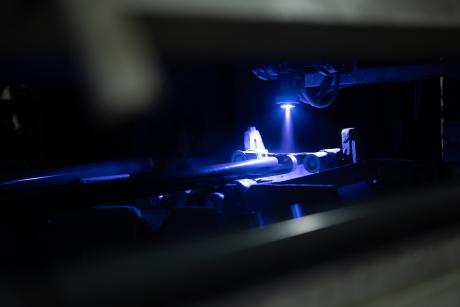
Types of Galvanizing for Conduit Threads
- Hot Galvanizing (Continuous Galvanizing Process)
- This method continuously coats steel with a precisely controlled spray of zinc, ensuring uniform coverage and optimal protection.
- The result is a smooth, even finish that prevents excess buildup, allowing conduit threads to remain functional and precise.
- Offers a reliable surface for further protective coatings, such as PVC or urethane.
- Hot Dip Galvanizing
- This process involves immersing fully fabricated steel components into a molten zinc bath.
- While it provides a thick zinc layer, the coating is often uneven, leading to excess buildup and drips that interfere with proper thread engagement.
- Hot dip galvanizing frequently clogs conduit threads, requiring contractors to rethread (also known as rechase) them before installation—a time-consuming and frustrating task.
- Variability in the coating thickness can create challenges in achieving proper conduit and fitting alignment.
- Cold Galvanizing (Zinc-Rich Coatings)
- Cold galvanizing, also known as zinc-rich painting, involves applying a zinc-based coating using a brush or spray.
- While it provides some protection against corrosion, it doesn’t fuse with the steel at a molecular level like hot galvanizing, making it less durable over time.
- The coating can wear off over time, particularly in harsh environments, leaving the threads vulnerable to corrosion.
- Provides the least durable protection compared to hot galvanizing processes.
The Pitfalls of Using Conduit with Threads That Aren’t Properly Galvanized
Conduit threads that lack proper galvanization can lead to a variety of installation and performance issues:
- Thread Corrosion – Unprotected threads are susceptible to rust, compromising electrical continuity and structural integrity.
- Difficult Installation – Threads with uneven or excessive zinc buildup make it harder to align fittings properly, leading to delays and added labor.
- Incompatibility with Protective Coatings – Without a properly applied zinc on the threads, interference with additional coatings like PVC on other portions of the product may occur, reducing overall corrosion resistance.
- Increased Maintenance Costs – Corroded or damaged threads often require replacement, adding unnecessary costs to long-term system maintenance.
The Plasti-Bond ProTECH Process: The Superior Choice for Conduit Threads
Plasti-Bond has developed an advanced approach to ensure conduit threads remain protected and installation-ready. After the PVC coating process, our ProTECH process utilizes a series of precision steps to maximize performance:
Laser Trimming – Removes excess PVC from the conduit ends to ensure a clean application.
Surface Preparation – Threads are chemically cleaned and mechanically prepared for optimal bonding.
Hot-Galvanizing with 3-Axis Robotic Arms – Ensures precise and uniform zinc application without clogging threads.
Clear Polyurethane Spray Coating – Adds an extra layer of protection, shielding the galvanized threads from corrosive attack.
This process guarantees that Plasti-Bond conduit threads remain smooth, functional, and installation-ready—eliminating the need for rework and ensuring a secure, long-lasting connection.
Why Plasti-Bond Is the Best Choice
For electrical contractors, efficiency and reliability are key. Plasti-Bond’s controlled galvanization process ensures a consistent zinc coating, free from irregularities, for superior corrosion resistance.
- Ease of Installation – Our smooth, controlled zinc coating eliminates the need for extra preparation, reducing labor costs.
- Consistent Quality – Continuous galvanizing results in uniform protection, ensuring that each length of conduit meets industry standards.
- Thread Integrity – A properly applied zinc coating prevents thread clogging and eliminates the need for rechasing, ensuring quick and seamless connections.
- Long-Term Corrosion Protection – With our ProTECH process, conduit threads remain clean, functional, and installation-ready—eliminating unnecessary rework and ensuring superior durability in the field.
By choosing Plasti-Bond, electrical contractors get conduit that is not only built to last but also designed for seamless installation, saving time, money, and frustration.